Guidelines To Not Follow About Ultrasonic Sensor
Vacuum functions are additionally not attainable with an Ultrasonic stage transmitter. Ultrasonic liquid degree sensors are sometimes housed in a single meeting combining the acoustic transmitter and receiver in a single system. So your complete meeting is weatherproof and could be simply slipped on and off the top of the stilling well pipe. I mounted the lid of a waterproof electrical conduit box to the highest of the PVC cap by drilling a hole huge sufficient for the sensor, which gets secured with a regular 3/4″ NPT nut. On the highest of the box I mounted a weatherproof 6v photo voltaic panel, which is routed into the field by way of a cable gland to keep the battery charged. Inside the box there’s a Seeduino Stalker datalogger board with Xbee radio and a LiPo battery. The photo voltaic panel retains the battery charged, so the batteries won't ever must be changed. You need an extended range ultrasonic so you can keep your pulse settings at a contented medium. The business in query will decide what kind of circulate meter will must be operated, as you can either use evasive or non-invasive units.
Accelerometer sensors often measure vibration or acceleration of various gadgets, such as motors, pumps, and many others. A piezoelectric sensor of this kind is often used to measure vibration of motor bearings, or other gadget, to determine the put on on the bearing in order that maintenance might be carried out earlier than t here is a catastrophic bearing failure. Sensors of this type responds only to living heat energy and is not going to triggered by sunlight or heating from ventilation system. Piezoelectric sensors convert a physical, acceleration, strain, or other input to an electrical sign that serves as an enter to a data processing system. motion sensor switch results in a response from the system. This system can yield a preprogrammed response that can control some side of the process by maintaining the operation within desired working parameters. Another group of piezo sensors function on the principle of measuring distance in a fluid, primarily by the usage of transit time measurements and a corresponding data processing system. Ultrasonic sensors handle distance measurement or position detection of granules, fluids and powders. Floor effects can be decreased by experimenting with the position of the system, installing within a stilling properly or wave guide, and some ultrasonic gadgets embrace options to minimise the effects of foaming, bubbles, vapour and turbulence.
This information along with information of the geometry of the vessel and the position of the sensor and the traits of the material within the bin allows for correct calculation of the amount of material in the bin. An additional benefit of a piezo sensor on this utility is that the piezo sensor beam isn't affected by dust within the bin that may outcome throughout the material charging operation. These sensors function by intermittently shooting a sound beam at the floor degree of the material within the bin, and receiving back the reflection of that sound beam because it reflects off of the floor. Piezo level sensors can decide the quantity of material remaining in a bin, and can be used to regulate the bin contents. One instance of such a piezo sensor is an accelerometer. Understanding the pace of the sound wave in air, and the transit time for this sound wave to travel to the fabric surface and back to the sensor, one can determine the distance of the fabric surface from the sensor. Low-power ultrasound, which is used for measuring distance (range finding), non-destructive checks, echography (ultrasound scanning) and sub-marine acoustics. Ultrasound liquid stage sensor technology transmits a excessive frequency sound wave pulse and receives the wave echo reflected off a liquid floor.
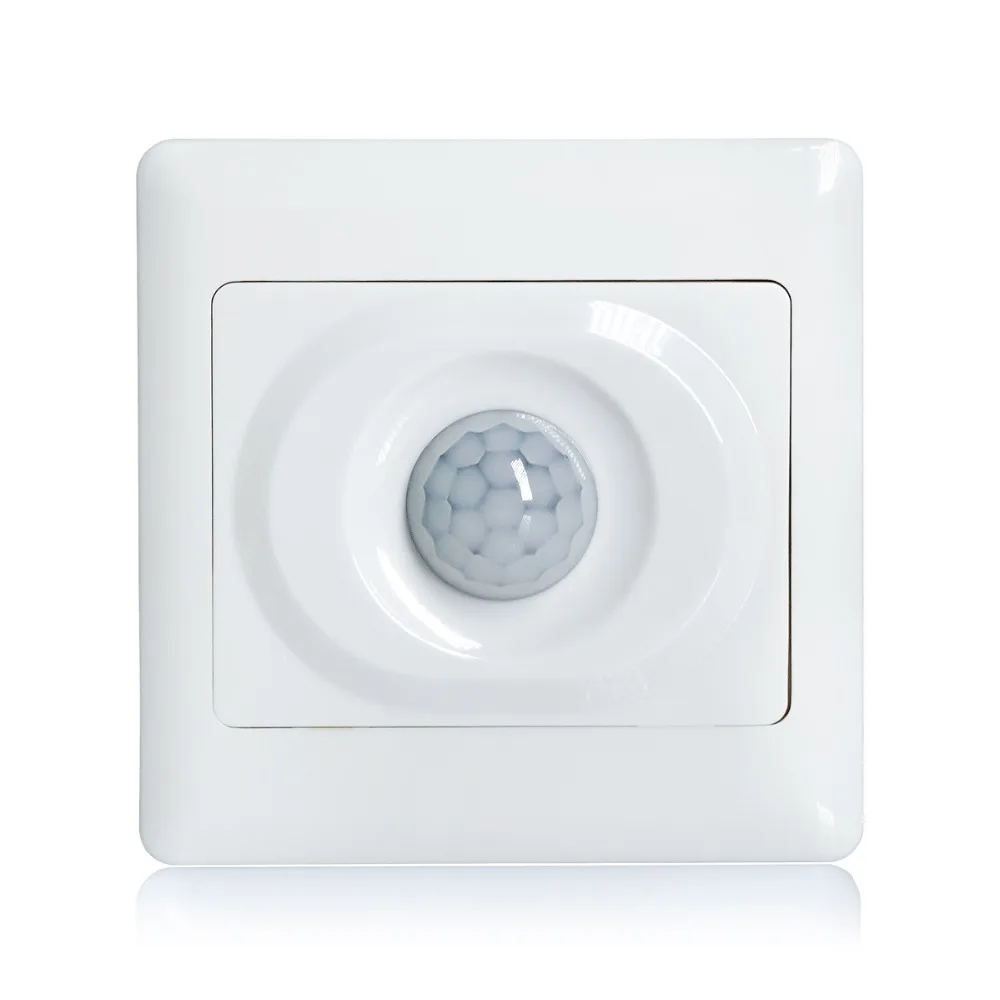
Ultrasonic liquid degree sensors are contactless measurement units which transmit and receive high frequency acoustic waves to measure the distance to the floor of a liquid based substance. The fusion of various or related sensors normally has a excessive calculation demand, which increases considerably with the area to be evaluated and the variety of sensors. The premise of the method is to use the truth that the areas to be evaluated principally face a slightly small number of obstacles, which cover a smaller percentage of the entire atmosphere. As a last step, we applied wavelet transformation to identify the regions of curiosity, the place the application of a refined raster is critical, and thus additional reducing the number of grid points the place the calculation must be carried out. In the current issues, we suggest a wavelet-based adaptive optimization method, which might greatly lower the number of grid points to be evaluated, and thus the mandatory computation time. This step can already end in a considerable decrease in the computation time, nonetheless with the transformation to polar coordinates, the tactic is not going to only be extra fitted to the issue to be solved, however the area of the evaluation can also be increased with the identical number of grid points.